Loading Guide - Dunnage
Loading Guide - Dunnage
National
Heavy
Vehicle
Regulator
This guide is part of a series of loading guides that provide tips and tricks to help you understand good load restraint. More detailed information on the principles covered by this guide can be found on page 192 of the Load Restraint Guide 2025.
What is Dunnage?
Dunnage is the packing placed under and between parts of the load.
Dunnage is generally made of either hard wood or soft wood timber and is either square or rectangular in cross-section.
Why use Dunnage?
When used correctly, dunnage can increase the effectiveness of the load restraint system and improve the safety for loaders, unloaders, and drivers.
Dunnage is used to:
- elevate the load to increase lashing angles
- increase the stability of the load
- separate parts of the load
- increase friction between the load and the deck, or between parts of the load
- allow for easier loading and unloading.
Types of dunnage may include:
- Softwood or hardwood, either square or rectangular.
- Anti-slip rubber placed between the load and the deck of the trailer to increase friction and reduce the number of lashings.
- Inflatable air bags which are placed inside containers or between loads to reduce any gaps between the loads.
Tips
Elevating the load using dunnage lessens the number of lashings required. The lower the lashing angle, the more lashings are required to give the same clamping force. One strap at 90° provides the equivalent clamping force to four straps at 15°.
Risks
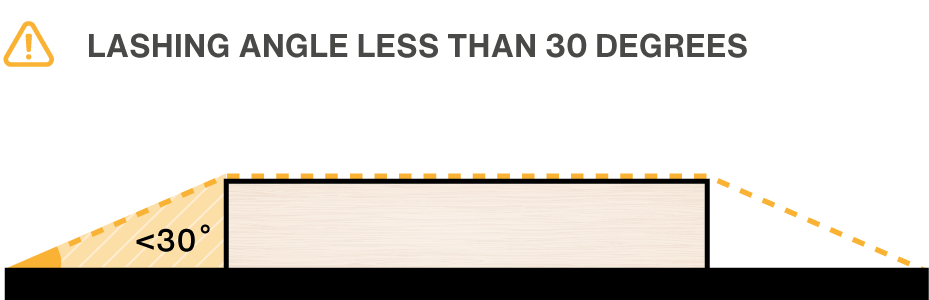
Good practice
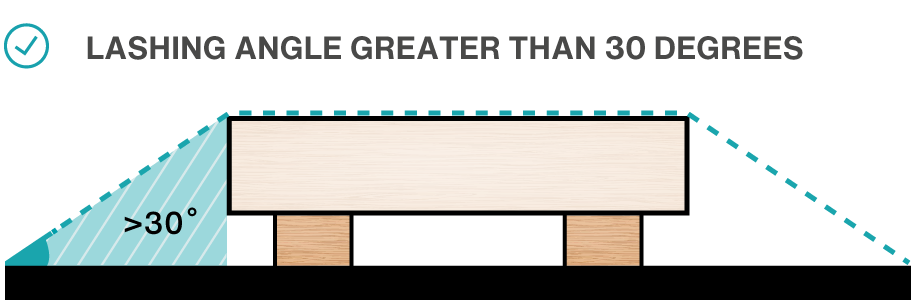
Any unused dunnage must be secured to prevent it falling from the vehicle. It’s important to align the dunnage with any lashing you apply to the load.
Risks
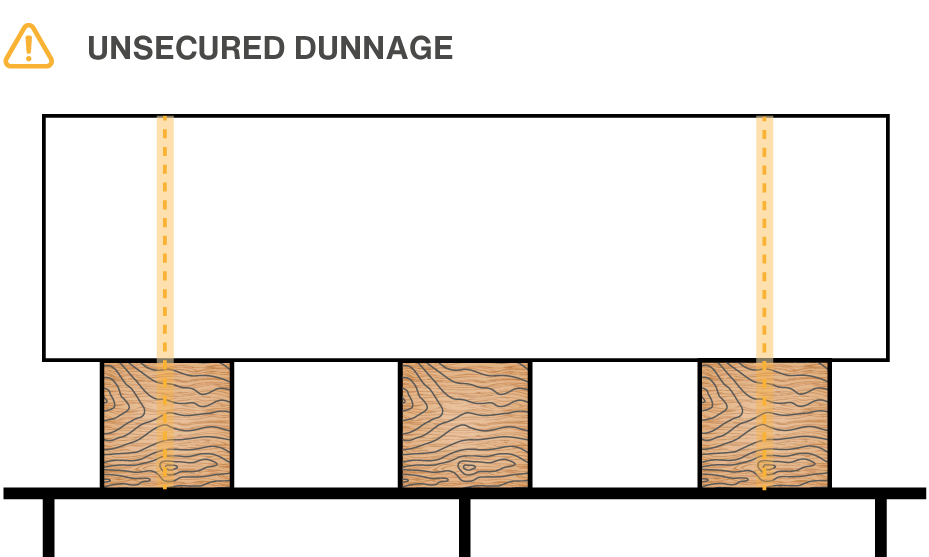
Good practice
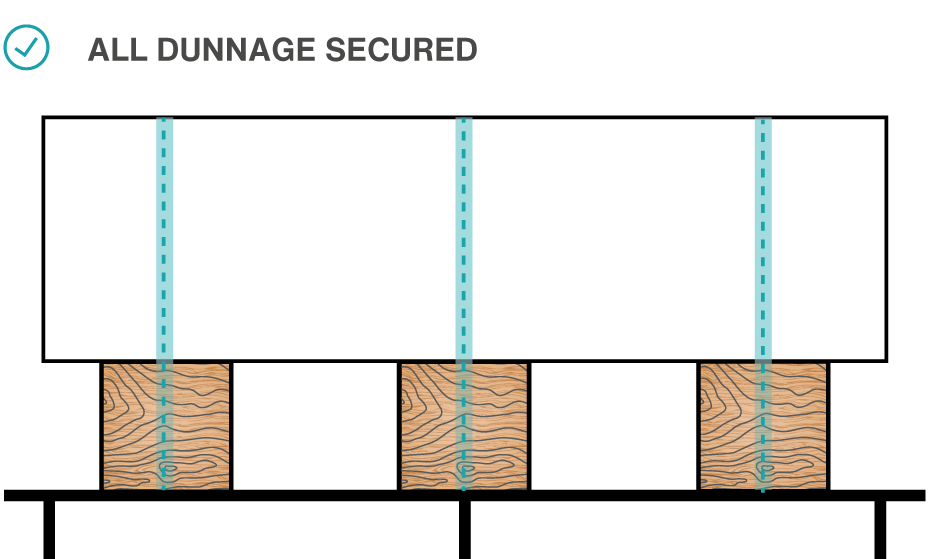
Do not stack pieces on top of each other (in parallel) because layers of dunnage can dislodge, resulting in a loss of lashing tension and restraint. Do not place dunnage on its narrow face because it can topple over, resulting in a loss of lashing tension and restraint. Excessively rounded corners on dunnage can roll under heavy deceleration/braking.
Risks
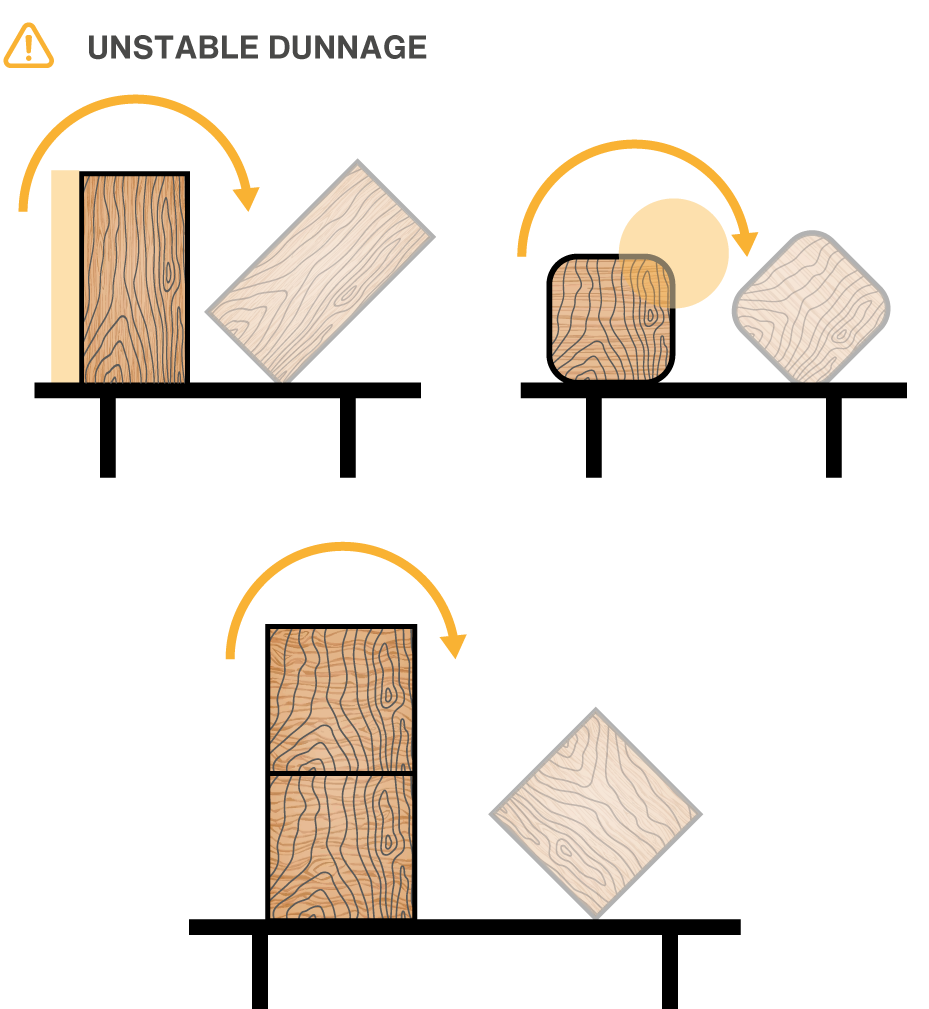
Good practice
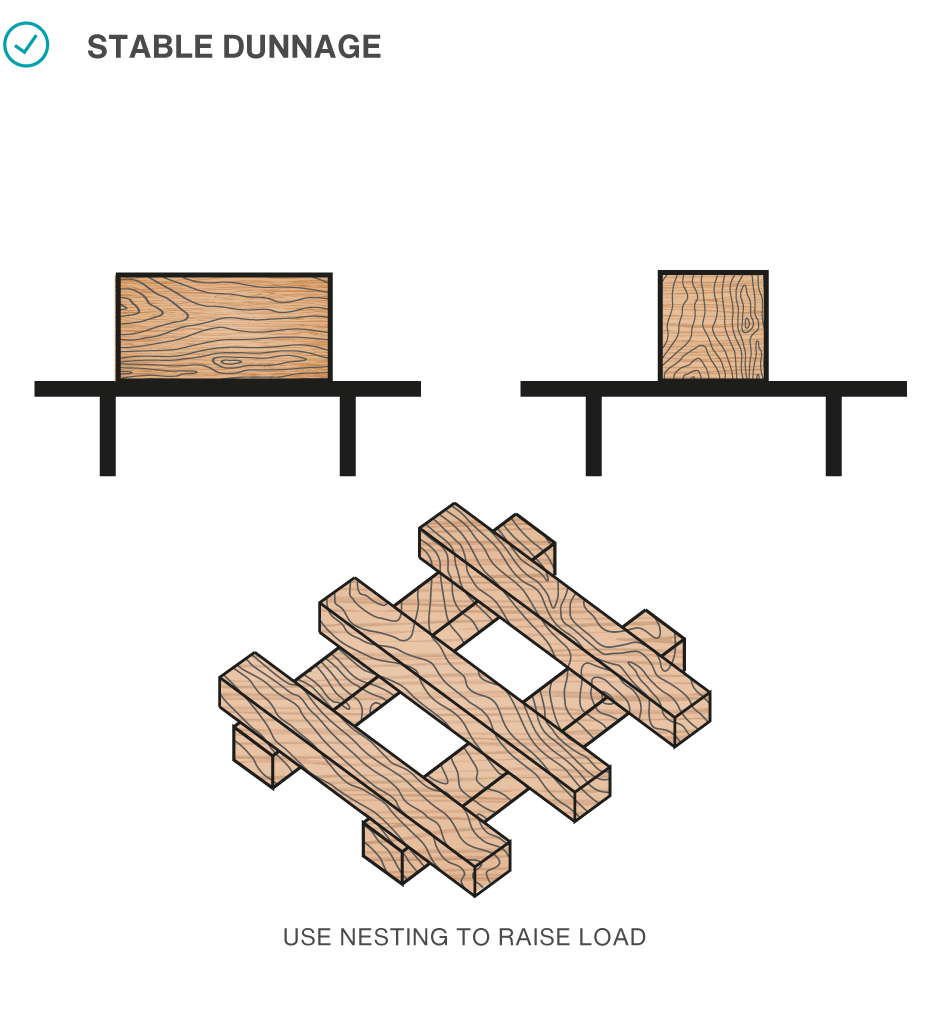
Make sure timber dunnage is relatively free of knots and splits, especially where the dunnage may span gaps, to reduce the risk of the timber splitting under load forces during transport.
Risks
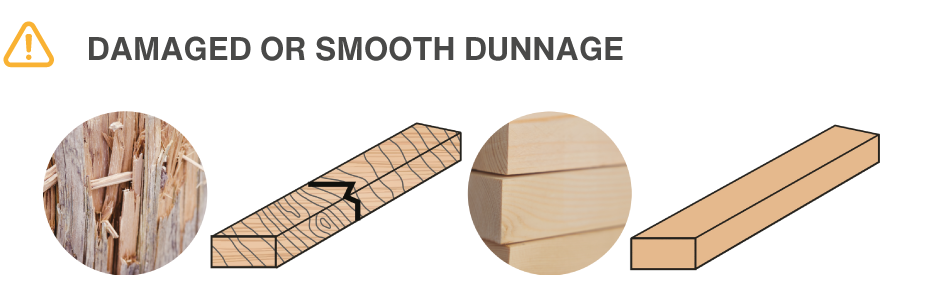
Good practice
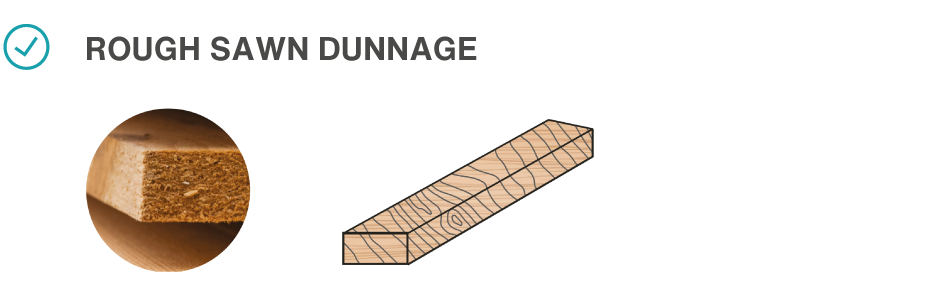
Case study
A heavy vehicle loaded with two packs of flat sheet steel weighing around five tonne each.
Dunnage was placed on its narrow face underneath and in between the packs of the flat plate steel.
When the driver applied the truck’s brakes when approaching a set of traffic lights, the dunnage rolled over causing a loss of lashing tension and restraint.
The two packs of flat sheet steel slid forward into the non-rated headboard, bending and breaking the tubular bars. Fortunately for the driver it didn’t contact the vehicles cab. However, if the load had shifted through and impacted the cab the result may have been serious injury or death to the driver.
This could have been avoided by using square dunnage or by placing the rectangular dunnage on its longer edge.
When relying on a non-rated headboard as part of the load restraint system, it should be braced with timber pallets/form plywood and chained to the combing rails to increase the strength.