Loading Guide - Shoring Bars
Loading Guide - Shoring Bars
National
Heavy
Vehicle
Regulator
This guide is part of a series of loading guides that provide tips and tricks to help you understand good load restraint. More detailed information on the principles covered by this guide can be found on page 88 of the Load Restraint Guide 2025.
What are shoring bars?
Shoring bars are high-strength bars that help reduce load movement during transport. They may also be called blocking bars, beams, or pogo sticks.
They are most commonly used within fixed-body vehicles and trailers.
Types of shoring bars
Shoring bars are either tubular or rectangular in shape and can be fitted horizontally or vertically.
They can be spring-loaded or have a ratchet mechanism that is used for locking in position.
What do shoring bars do?
Shoring bars form part of a load restraint system and stabilise a load from moving or shifting during transport.
Shoring bars may provide restraint for both forward and rearward direction however have limited capacity and additional restraint may be required.
It is critical not to overload shoring bars and multiple bars may be required in multiple locations along the load to control movement.
How are shoring bars used to restrain a load?
Shoring bars can form part of an effective load restraint system for some loads.
Depending on the weight of the load, they may need to be installed every pallet row, every second, every third, etc.
For loads on pallets that are not suitably unitised it’s advisable to use plywood or similar material between the load and bars to ensure they are effective at restraining the load, preventing its movement.
Ensure you understand the capacity of shoring bars and follow the manufacturer’s guidance so the rated capacity is not exceeded, they are installed appropriately and bars and tracks are not damaged.
Tips
To prevent a failure of the load restraint system, always install and use shoring bars as the manufacturer intended.
Only blocking the rear of the load may exceed the rated capacity of the shoring bars and may result in a load restraint system failure. Block every row or every second row as required.
Risks
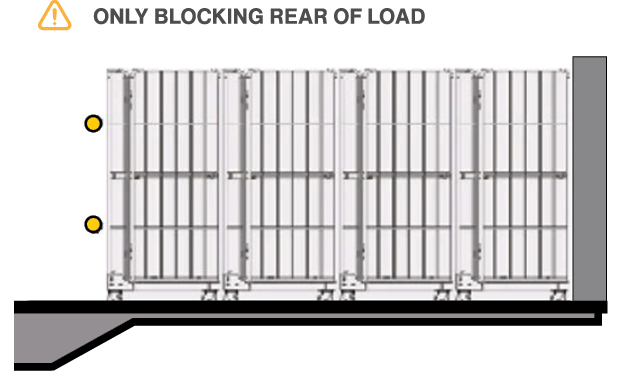
Good practice
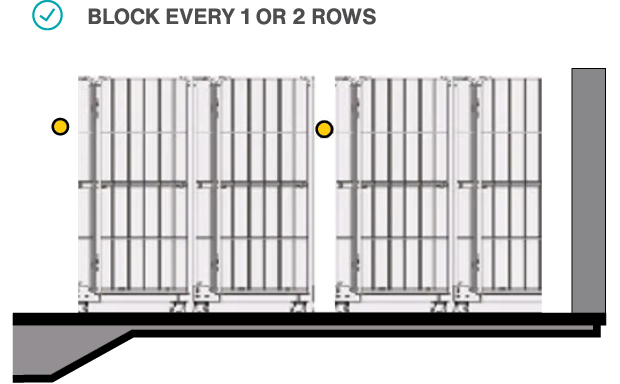
Only using one shoring bar may exceed its rated capacity. Always use both the upper and lower shoring bars and tracks to restrain load if available.
Risks
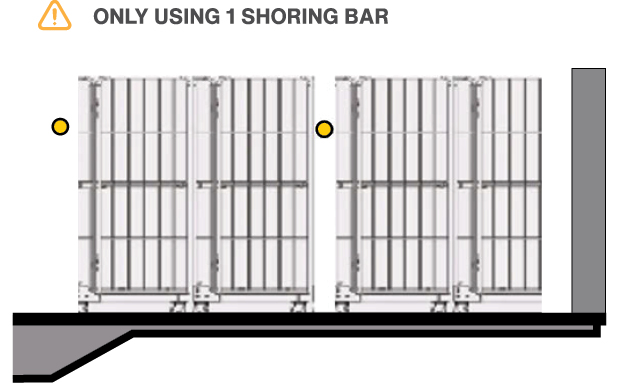
Good practice
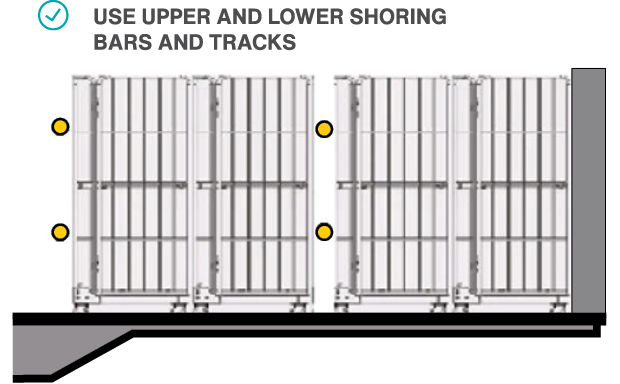
Do not use damaged or worn track as the bars may fall out during transport. Only use straight and undamaged tracks.
Risks
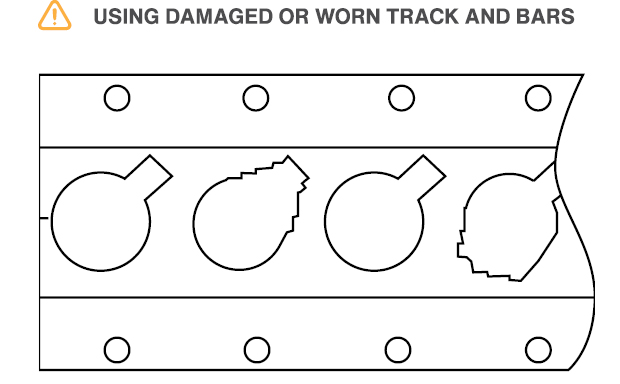
Good practice
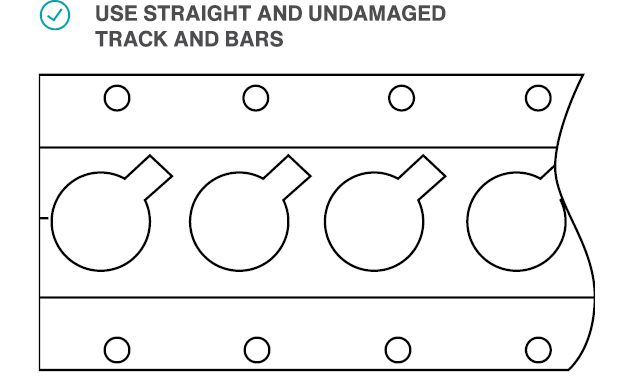
Incorrectly installed shoring bars will reduce their rated capacity and may fail. Check with the manufacturer for the correct installation procedure.
Risks
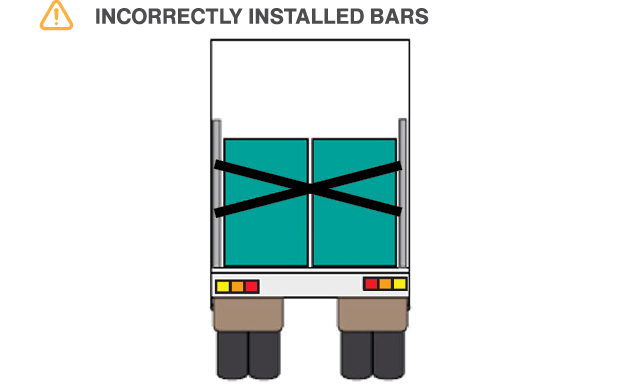
Good practice
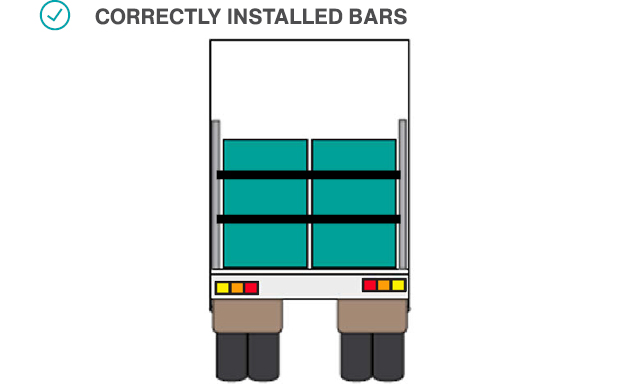
Case study
This is what can happen when shoring bars are not used or correctly installed.
Milk is often carried on trollies with wheels to help with manual loading and unloading.
Possible causes of failure include:
- Brakes not applied on wheeled trollies
- Not installing enough shoring bars down the length of the load
- Only installing shoring bars at the rear of the load
- Shoring bars or tracks damaged or worn
- Excessive gaps between the load and the shoring bars
- Not spreading the load by using plywood or other material.
If there are large gaps, the load will move forwards and rearwards on every gear change, braking application, acceleration, or change in the road gradient, leading to failure of equipment and the load restraint system.
Rear doors and walls have failed due to a ramming effect of the load against the rear doors caused by the excessive movement of the load.